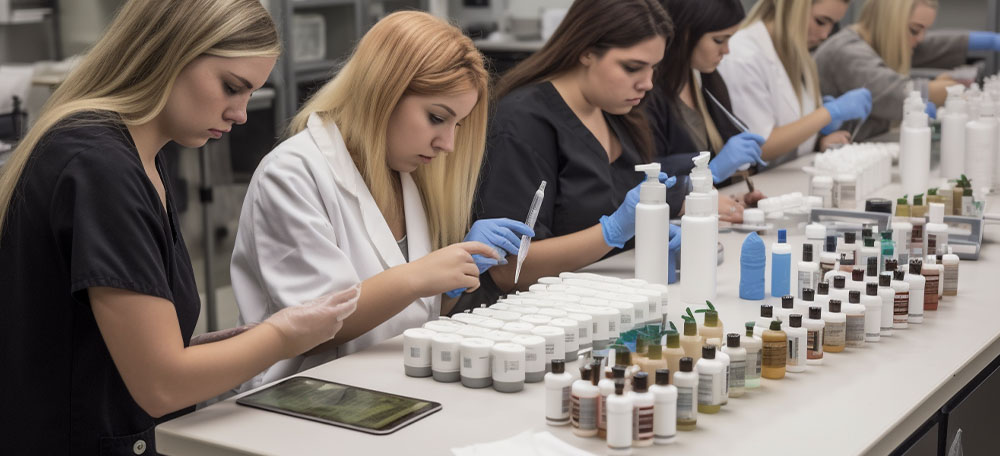
The beauty industry constantly evolves, with new products and manufacturing processes developed daily. As a contract manufacturer for beauty brands, we at More Naturals understand the importance of staying up-to-date on these advancements to provide our clients with the best possible outcomes. However, understanding the differences between cosmetic product manufacturing processes can be particularly confusing for those outside the industry.
Several methods are used to create cosmetic products, each with its unique benefits and drawbacks. From traditional batch processing to newer continuous processing techniques, knowing which method will work best for your specific needs is essential before beginning production. This article explores some of the most common cosmetic product manufacturing processes and what sets them apart. By gaining a deeper understanding of these methods, you’ll be better equipped to make informed decisions when creating high-quality beauty products that stand out in today’s competitive market.
Traditional Batch Processing
Traditional batch processing is a standard manufacturing method in the cosmetic industry. It involves mixing raw materials in batches, which are then processed and packaged for sale. One of the benefits of traditional batch processing is that it allows for greater quality control over each batch, helping to ensure consistency across products. In addition, this method offers flexibility, as manufacturers can adjust formulas and quantities depending on demand.
However, there are some drawbacks to traditional batch processing. The process can be time-consuming, with long lead times between production runs. If demand suddenly increases, manufacturers may struggle to keep up with customer orders. Additionally, traditional batch processing can result in higher costs due to the need for specialized equipment and labor.
Compare traditional batch, continuous, and semi-batch processing methods in cosmetic manufacturing. Discover their unique advantages and disadvantages.
Traditional batch processing is essential for high-quality cosmetics, but new techniques offer efficiency and cost benefits. Explore continuous processing in our subsequent section.
Continuous Processing
As the beauty industry constantly evolves, contract manufacturers must keep up with the latest technology and innovations to provide exceptional products. Continuous processing is one manufacturing process gaining popularity due to its efficiency advantages. This method offers a streamlined approach to producing large quantities of cosmetic products while maintaining consistency.
In continuous processing, ingredients are continuously fed into the production line without interruption, resulting in a smooth flow of materials. This eliminates the need for batch-to-batch adjustments and reduces downtime between batches. As a result, this type of manufacturing leads to increased productivity and reduced waste.
At More Naturals, we understand that our clients demand high-quality products with consistent results. Continuous processing allows us to achieve just that by ensuring every product meets strict quality standards from start to finish. Additionally, this method allows for more effortless scalability when increasing production volumes, as there is no need to adjust individual batches.
Continuous processing provides numerous benefits over traditional batch methods, including higher efficiency and better product consistency. More Naturals’ implementation of continuous processing delivers unparalleled value for brands looking for innovative solutions in their manufacturing processes.
Advantages:
- Increased productivity
- Faster turnaround times
- Reduced downtime between batches
- Greater control over ingredient ratios
- Reduces variations in finished products
- Ensures consistently high-quality output
With all these advantages considered, it’s clear why continuous processing has become an increasingly popular option among beauty brands worldwide. In addition, hot pour manufacturing is following up on our tour through different manufacturing processes – another exciting innovation within cosmetic product creation!
Hot Pour Manufacturing
Continuous processing produces cosmetic products that involve the continuous flow of materials rather than batch processing. While it has its advantages in speed and efficiency, there are limitations to what can be achieved using this method. Another manufacturing process that may be more suitable for certain types of cosmetics is hot pour manufacturing.
Hot pour manufacturing involves melting raw ingredients and pouring them into molds or containers while they are still liquid. This method allows for greater control over the temperature and viscosity of the mixture, which can result in a more consistent product with fewer defects. It also eliminates the need for preservatives, as the high temperatures used during production help to sterilize the product.
One of the main benefits of hot pour manufacturing is that it can produce higher quality products than traditional batch processing methods. Because each ingredient is melted separately before being mixed, there is less contamination or uneven distribution risk. Additionally, manufacturers can produce larger quantities faster without sacrificing quality since there is no waiting time between batches.
Compared to traditional batch processing methods, hot pour manufacturing offers several advantages. For one thing, it requires less equipment and space than other forms of production because all ingredients are combined in a single vessel. In addition, hot pour manufacturing typically produces less waste because unused material can be re-melted and reused.
Cold Processing
Choose the right manufacturing process for high-quality cosmetics. Explore cold processing, a method that preserves ingredients without heat or chemicals.
The benefits of using cold processing in cosmetics include preserving the efficacy of natural ingredients that may be damaged by heat exposure during traditional manufacturing processes. This results in more potent products that retain their beneficial properties. Additionally, since no heat is used, there’s less chance of damaging or degrading sensitive compounds like vitamins and antioxidants in many natural extracts.
However, with every benefit comes some drawbacks. For example, cold processing takes longer than other methods as it requires time for proper emulsification of ingredients. It also has limited application for specific formulations because not all ingredients can be mixed effectively through this process. As a result, manufacturers must carefully consider whether cold processing suits each product they produce.
In conclusion, cold processing offers benefits such as retaining potency and avoiding damage to sensitive compounds when creating skincare products with natural-based formulas. However, it has limitations due to compatibility issues between certain ingredients. Still, More Naturals continues to explore innovative ways of incorporating this technique into our cosmetic manufacturing processes alongside others like emulsion manufacturing.
Emulsion Manufacturing
In cosmetic product manufacturing, emulsions are essential to lotions and creams. They combine two immiscible liquids blended to form a homogenous mixture. The most common emulsion type is oil-in-water (O/W), which involves blending water into the oil phase. There is also a water-in-oil (W/O) emulsion, where the oil is mixed with water.
Formulation considerations play a critical role in producing stable emulsions. Several factors must be taken into account when developing O/W or W/O formulations. These include selecting appropriate surfactants, choosing the proper viscosity modifiers, incorporating preservatives, and determining the antioxidants’ needs. Additionally, it’s crucial to consider the pH level of each ingredient, as different values can affect stability. Finally, formulations should be tested for compatibility before beginning production.
Stability testing is another crucial aspect of emulsion manufacturing that cannot be overlooked. Stability tests involve examining how much change occurs in the appearance or consistency of the formulation over time under various conditions, such as temperature fluctuations and exposure to light or air. Performing these tests during development and after full-scale production is recommended because changes may occur due to storage environments during transportation.
Creating stable emulsions requires thoroughly considering formulation ingredients and their interactions and rigorous stability testing throughout development until final products reach consumers. In our subsequent section about vacuum emulsification methodology, we will discuss how this process further aids in achieving successful results by ensuring proper mixing techniques while maintaining safe working environments simultaneously through its unique approach toward cosmetics processing technology advancements.
Vacuum Emulsification
Vacuum emulsification is a widely used process in the cosmetic industry that uses vacuum technology to create stable and uniform mixtures. This method has become increasingly popular due to its ability to produce high-quality products with excellent texture and viscosity, making it a go-to option for many manufacturers.
One of the significant advantages of vacuum emulsification is its ability to reduce air bubbles in the product. Removing excess air leads to a more consistent mixture, which translates into better quality and longer shelf life. Furthermore, this method reduces oxidation, an important factor when creating products sensitive to light or heat.
Despite its numerous benefits, there are limitations associated with vacuum emulsification. One such limitation is that it requires specialized equipment and expertise, which can increase production costs significantly. Additionally, because this process uses higher temperatures than other methods like cold processing or blending, it may not be suitable for all formulations.
When considering cost comparisons between manufacturing processes, one must consider several factors beyond initial investment costs. Other variables, such as material waste reduction and energy consumption, can significantly affect sustainability efforts. For example, vacuum emulsification typically generates less waste than traditional mixing methods but may require more energy usage due to specialized machinery requirements.
Choosing the proper method for your needs depends on criteria such as formula complexity, raw materials selection, target market demographic, and environmental impact goals. By partnering with contract manufacturers specializing in multiple manufacturing techniques like More Naturals, brands can access diversified insights and expert guidance towards optimizing their competitive advantage while minimizing carbon footprint during production, irrespective of chosen formulation technique.
Choosing The Right Method For Your Needs
Vacuum emulsification is a widely used manufacturing process in the cosmetic industry that provides excellent stability and uniformity of products. However, it may not always be the best method for every brand or product type. More Naturals understands the importance of custom formulation to meet clients’ specific requirements and preferences, so we offer various options for cosmetic product manufacturing processes.
Choosing the proper method for your needs involves considering several factors, such as the ingredients used, desired texture and consistency, production capacity, and budget. Our team at More Naturals works closely with our clients to determine their unique needs and recommend suitable methods based on industry standards. We take pride in offering flexible solutions catering to small-scale startups and large established brands.
In addition to providing high-quality custom formulations, More Naturals also prioritizes quality control and safety measures during every step of the manufacturing process. This includes thorough testing of raw materials before use, strict adherence to hygiene protocols in our facility, regular equipment maintenance checks, and final product testing before release. Our commitment to these measures ensures that all products we manufacture are safe, effective, and compliant with industry regulations.
At More Naturals, we recognize the significance of selecting an appropriate cosmetic product manufacturing process tailored to individual client specifications without compromising safety and quality standards. As a global contract manufacturing leader for beauty brands, we remain committed to delivering superior services through innovation while maintaining high-quality assurance levels across all production aspects. In the next section about ‘quality control and safety measures,’ we will discuss how we ensure optimal results throughout each production stage through rigorous monitoring techniques.
Quality Control And Safety Measures
Quality control and safety measures are crucial to the cosmetic product manufacturing process. At More Naturals, we understand that our clients demand high-quality products that meet regulatory compliance standards. To achieve this, we have established comprehensive testing protocols to ensure consistent quality throughout the production cycle.
Our first step in maintaining quality is sourcing ingredients from reliable suppliers who follow strict quality control procedures. We then conduct internal tests to verify the purity and potency of each ingredient before using them in our formulations. Finally, our team of experts conducts regular checks on every batch produced to ensure they conform to our rigid specifications for texture, color, scent, and efficacy.
To guarantee consumer safety, we adhere strictly to industry regulations regarding labeling requirements, expiration dates, and storage conditions. In addition, we subject all finished products to rigorous third-party testing by independent laboratories specializing in microbiological analysis and toxicology assessments.
Following these stringent processes results in a line of safe-to-use, superior-quality beauty products trusted by consumers worldwide. As an innovative contract manufacturer working with some of the most forward-thinking brands in the industry today, we take pride in delivering exceptional results at every stage of development – from ideation through formulation and final production.
- Quality assurance.
- Consumer confidence.
- Trustworthiness.
Conclusion
Manufacturing cosmetic products can significantly impact their quality, consistency, and safety. Understanding the differences between various methods is crucial for choosing the right one that meets your needs. For example, traditional batch processing involves mixing ingredients in large batches before filling containers, while continuous processing uses a constant flow of ingredients to create products faster. In addition, hot pour manufacturing melts ingredients together, while cold processing avoids heat to preserve the integrity of natural ingredients.
Emulsion manufacturing combines oil and water-based ingredients, while vacuum emulsification utilizes pressure to blend them evenly. When selecting a method, it is essential to consider factors such as product formulation, production volume, and desired texture and viscosity. Additionally, implementing rigorous quality control measures and adhering to safety regulations ensures consistent results and protects consumers from harm.
At More Naturals, we prioritize transparency and safety in all our manufacturing processes. Our team works closely with clients to understand their unique needs and recommend the most suitable method for producing high-quality beauty products efficiently. Through our commitment to innovation and excellence, we strive to help brands positively impact people’s lives and the environment.